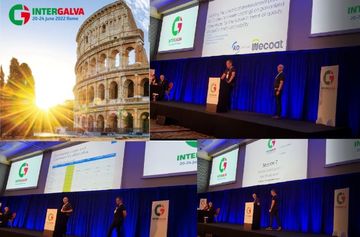
AD Chemicals et WeCoat préparent le processus de thermolaquage HDG Duplex pour l'avenir
Transition vers le prétraitement au chrome-3
WeCoat applique un thermolaquage sur l'acier galvanisé depuis 1980 et fournir la plus haute qualité a toujours été une priorité absolue. Innover et contribuer à un monde meilleur entrent également dans cette ligne de conduite. En 2016, WeCoat a implémenté un prétraitement au chrome-3 d'AD Chemicals, ce qui en fait l'un des premiers thermolaqueurs sur acier galvanisé à réussir à garantir la plus haute qualité en termes d'adhérence de la peinture et de protection contre la corrosion avec un système sans chrome(VI) qui répond à la classe C3-C4-C5. WeCoat dispose d'un prétraitement chimique au cours duquel une couche de conversion est appliquée sur le produit galvanisé. Cette opération est suivie d'un thermolaquage en 1 ou 2 couches.
Le tableau ci-dessous, basé sur les normes GSB, donne un aperçu des différentes possibilités avec la qualité maximale réalisable. WeCoat et AD ont remporté le prix de l'innovation ION Borghardt pour cette innovation.
Plusieurs revêtements en zinc
Chaque installation de galvanisation à chaud possède son propre processus de galvanisation avec des propriétés spécifiques. C'est pourquoi il existe sur le marché un large éventail de revêtements en zinc différents composés de différents éléments d'alliage. Il est important de tenir compte de ces propriétés lors du développement d'un processus de prétraitement chimique.
Les principales différences dans le revêtement en zinc concernent principalement les éléments PB, Bi, Ni, Al, Mn, Si, mais la composition et l'épaisseur du matériau de base ont également une grande influence sur les propriétés finales. En particulier avec des teneurs en Si plus élevées, des épaisseurs de paroi et des soudures plus importantes, les couches inférieures remontent à la surface et la teneur en Fe est plus élevée qu'avec un acier MC, par exemple. Ce que nous voyons, c'est qu'en fonction du matériau de base et des éléments d'alliage, la structure va d'une surface brillante très lisse à une surface terne avec une structure très ouverte.
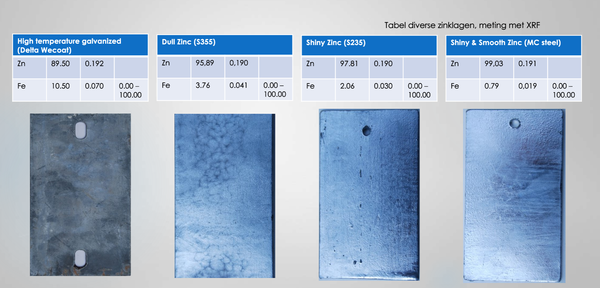
Ajustements du processus sur les revêtements en zinc
Afin de traduire la diversité de ce qui précède en un processus robuste, un long chemin de tests a été parcouru. Ces tests ont permis de conclure qu'il n'y a pas d'influence directe des éléments d'alliage. Dans tous les alliages testés, il est possible d'obtenir une adhérence parfaite.
Cependant, les éléments d'alliage influencent la composition et l'épaisseur des revêtements en zinc. Le résultat, à savoir ce qu'un client reçoit de l'installation de galvanisation, peut être très varié en termes de surfaces. La composition utilisée ne fait donc aucune différence.
Ce qui fait la différence, c'est la structure de la surface, qui varie en raison des différents composants d'alliage. Avec l'acier MC galvanisé en Zn-0,25PB-0,1Bi-0,004%Al ou Zn-0,25Pb-0,1Bi-0,04%Ni-0,004%Al, il se forme un revêtement en zinc très lisse, brillant, homogène et à grandes fleurs. Sur l'acier S355 de la même épaisseur de base, on observe un revêtement épais et sombre avec une structure plus ouverte (qui est influencée par les éléments d'alliage). Les deux situations sont obtenues avec chaque fusion similaire. La différence de prétraitement réside dans le fait que le revêtement en zinc brillant doit être décapé beaucoup plus longtemps que l'acier S355 terne lorsqu'on utilise le même bain de décapage avec les mêmes paramètres. Pour le zinc lisse et brillant, un minimum de 2 g/m² est requis. Pour les autres matériaux, un temps plus court est suffisant, auquel cas il faut aussi 2 grammes/m². Le temps de traitement du zinc lisse et brillant peut atteindre un facteur de 4 ou 5 fois le temps de traitement d'un matériau galvanisé terne.
Les temps exacts ne peuvent pas être déterminés de manière générique, car ils dépendent de la température, de la projection ou du trempage, etc. Le facteur d'un temps 4-5 fois plus long pour un matériau brillant reste valable aussi bien pour le trempage que pour la projection.
La grande différence est due au fait qu'avec un matériau terne, la réaction commence immédiatement et qu'avec un matériau brillant, la réaction commence très lentement. Le décapage avant l'application de la couche de conversion est donc de loin l'étape la plus importante à contrôler. Tous les autres bains de traitement et de rinçage doivent être propres, conformément aux exigences de qualité du fournisseur de produits chimiques.
Optimisation du processus de thermolaquage
Au sein de WeCoat, nous utilisons principalement des poudres accréditées GSB, tant à cuisson normale qu'à basse cuisson, provenant de fournisseurs renommés. On obtient ainsi les bonnes propriétés de la poudre et on dispose d'une base constante pour définir les processus de manière appropriée.
WeCoat a constaté que des problèmes d'adhérence se posent lorsque des matériaux fins de moins de 2 mm sont émaillés dans un four continu à 190°C. La phase d'écoulement de la poudre est alors très courte en raison de la courbe de chauffe rapide du matériau mince. Les courbes de durcissement sont initialement adaptées pour passer d'un processus continu à un processus par lots.
Cela permet à WeCoat d'abaisser la température entre les lots. En démarrant le lot avec une température de départ plus basse, on peut prolonger la phase d'écoulement, c'est-à-dire la phase où les poudres forment la liaison avec le substrat, pour des poudres normales entre 120°C et 140°C.
Préparer le processus pour l'avenir.
La nouvelle directive européenne sur les objectifs climatiques pour 2030 aura un impact majeur sur l'ensemble de l'industrie de la galvanisation. C'est pourquoi WeCoat et AD Chemicals ont lancé une deuxième phase d'innovation du procédé Duplexcoat. Lors de cette deuxième phase d'optimisation, nous avons cherché des moyens de rendre le processus de revêtement Duplex plus durable en économisant l'électricité, le gaz, les produits chimiques, l'eau et les coûts de maintenance.
La consommation d'énergie la plus importante dans le processus de prétraitement est la suivante :
• Bain de dégraissage à 60°C
• Four de thermolaquage à 190°C.
Principale consommation de produits chimiques et eaux usées :
• Bain de dégraissage (eau)
• Bain de décapage (chimique).
Réduire la température de la zone de dégraissage
La plupart des galvanisateurs travaillent avec des bains de dégraissage à 60°C. En réduisant cette température tout en conservant la même capacité de dégraissage, on peut réaliser des économies considérables sur les coûts énergétiques.
Par conséquent, WeCoat a fixé l'objectif suivant en collaboration avec AD : réduire la température du bain de dégraissage. C'est surtout dans l'installation de projection où la chimie se refroidit rapidement pendant la projection et où beaucoup d'eau s'évapore que les économies seront les plus importantes. Il s'agissait d'un objectif ambitieux et de nombreux essais ont été nécessaires dans les laboratoires d'AD, mais le résultat final est un bain de dégraissage qui peut fonctionner à 35 °C. Le bain est utilisé depuis six mois et WeCoat peut constater que la réduction des pertes de vapeur entraîne à elle seule une réduction de 30 % de la consommation d'énergie.
Des économies d'énergie globales de plus de 60% sur le bain de dégraissage ont été réalisées avec une consommation d'eau réduite de 30%. Un autre avantage est l'amélioration des conditions de travail : l'exposition due à la perte de vapeur est considérablement réduite, ce qui permet de réaliser des économies sur la consommation d'eau mais aussi sur la préservation du bâtiment et des équipements environnants.
Optimiser le processus de durcissement
Des améliorations ont également pu être apportées au processus de thermolaquage afin d'optimiser le processus. WeCoat est passé de la norme 190°C en continu au lot combiné à un système de suivi et de contrôle intégré intelligent. Voir également les images jointes pour plus de précisions.
Lorsque les rayons entrent et sortent, la température est réglée à 120°C et les ventilateurs passent à environ 10%. Il en résulte ce qui suit : le niveau de température dans le four est maintenu, par conséquent, le nouveau matériau peut aller directement dans le four de cuisson sans passer d'abord dans le four électrique pendant que le lot précédent est en train de durcir. Résultats :
• Four électrique à économie d'énergie : 100% (éteint)
• Four ordinaire à économie d'énergie (gaz) : 30%
Optimisation du bain de décapage
Un phénomène normal des bains de décapage pour le zinc est que la teneur en zinc du bain augmente rapidement. Les bains de décapage doivent contenir un maximum de 5 grammes de zinc par litre, sinon les performances diminueront. La surveillance de la quantité de zinc est donc très importante. La solution de décapage contaminée (acide) doit être traitée dans la station d'épuration des eaux usées et le bain de décapage doit être régulièrement réapprovisionné en produit de décapage frais pour maintenir le bain de traitement dans les paramètres.
C'est pourquoi WeCoat et AD ont entamé un processus de développement pour améliorer la durée de vie du bain de décapage. On a trouvé la solution dans un système intelligent de régénération et de filtration. En bref, une installation sépare le zinc de l'acide dans un système fermé avec le bain de décapage. On peut ensuite réutiliser la solution de décapage filtrée dans la ligne de prétraitement chimique.
Les résultats de ce système sont clairs : économies d'eau, moins de calcaire et économies supplémentaires de la soude caustique nécessaire au processus de traitement des eaux usées.
Bien qu'un investissement en équipement soit évidemment nécessaire pour adapter le processus à cette façon de travailler, il existe plusieurs avantages majeurs :
• Réduction de 80 % des coûts de traitement des eaux usées
• 20-100K d'économies pour un processus moyen de revêtement duplex.
Conclusion
WeCoat et AD ont réussi ensemble à réaliser une série d'améliorations grâce à l'innovation et à l'expertise commune, ce qui a donné lieu à l'aperçu des économies suivantes :
• Remplacement du chrome (VI)
• Économies réalisées sur les plans suivants :
- Traitement des eaux usées
- Eau de traitement
- Consommation de produits chimiques
- Énergie
AUTEURS : Roland Van Meer (r.vanmeer@adinternationalbv.com) & Norbert Beljaars
PLUS D'INFORMATIONS : https://www.adinternationalbv.com/nl/