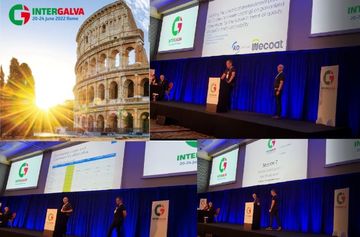
AD Chemicals en WeCoat maken HDG Duplex poedercoatproces klaar voor de toekomst
TRANSITIE NAAR CHROOM-3 VOORBEHANDELING
Firma WeCoat, het nieuwe Weert Groep, poedercoat vanaf 1980 op verzinkt staal waarbij sinds de start van het bedrijf altijd het leveren van de hoogste kwaliteit top prioriteit heeft gehad. Innoveren en bijdragen aan een betere wereld horen daar ook bij. Zo implementeert WeCoat in 2016 een chroom-3 voorbehandeling
van AD Chemicals en is daarmee een van de 1e poedercoaters op verzinkt staal die erin slaagt de allerhoogste kwaliteit op het vlak van lakhechting en corrosiebescherming te borgen met een chroom(VI)- vrij systeem dat voldoet aan de C3-C4- C5 klasse. WeCoat heeft een chemische voorbehandeling waarin een conversielaag wordt aangebracht op het verzinkte product. Dit wordt gevolgd door een 1 of 2 laags poedercoating.
In onderstaande tabel vanuit de GSB norm wordt een overzicht gegeven van de verschillende mogelijkheden met de maximaal haalbare kwaliteit. WeCoat en AD wonnen voor deze innovatie destijds de ION Borghardt innovatieprijs.
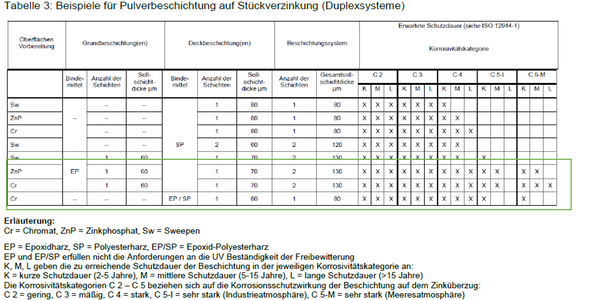
DIVERSE ZINKLAGEN
Iedere thermische verzinker heeft een eigen verzinkproces met specifieke eigenschappen waardoor er in de markt een breed scala aan verschillende zinklagen beschikbaar is bestaande uit verschillende legeringselementen. Het is belangrijk deze eigenschappen mee te nemen wanneer een proces voor chemisch voorbehandelen wordt ontwikkeld.
De belangrijkste verschillen in de zinklaag zitten voornamelijk in de elementen Pb, Bi, Ni, Al, Mn, Si, maar ook de samenstelling en dikte van het basismateriaal heeft grote invloed op de uiteindelijke eigenschappen. Met name bij hogere Si-gehaltes, grotere diktes en lasnaden groeien de onderlagen tot het oppervlak en is het Fe gehalte hoger dan bijvoorbeeld bij een MC staal (d.i. thermomechanisch gewalst staal). Wat we zien is dat de structuur, afhankelijk van basismateriaal en legeringselementen, zich beweegt tussen een zeer glad blinkend oppervlak, tot een dof oppervlak met een erg open structuur.
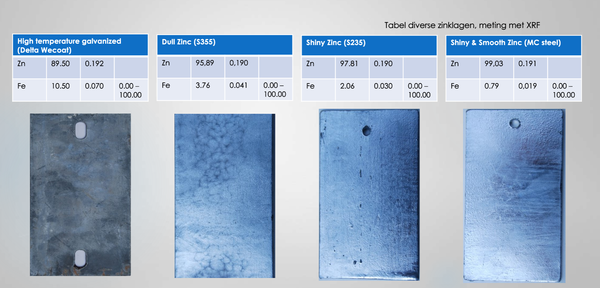
PROCESAANPASSINGEN OP ZINKLAGEN
Om de diversiteit van bovenstaande te vertalen naar een robuust proces is een lange weg van testen afgelegd. Vanuit deze testen is geconcludeerd dat er geen rechtstreekse invloed is vanuit de legeringselementen. Bij alle geteste legeringen is het mogelijk een perfecte hechting te verkrijgen.
De legeringselementen beïnvloeden echter wel de samenstelling en de dikte van de zinklagen. Het resultaat hiervan, wat een klant aangeleverd krijgt vanuit de verzinkerij kan heel divers zijn qua oppervlak.
Het maakt dus geen verschil welke samenstelling er gebruikt is.
Wat wel uitmaakt is de oppervlaktestructuur die varieert door de verschillende legeringsbestanddelen. Bij MC staal verzinkt in Zn-0.25Pb-0.1Bi-0.004%Al of Zn- 0.25Pb-0.1Bi-0.04%Ni-0.004%Al vormt zich een zeer gladde, blinkende, homogene zinklaag met grote bloemen. Bij staal S355 van dezelfde basisdikte is een dikke donkere laag met een meer open structuur (die wordt beïnvloed door de legeringselementen)
zichtbaar. Beide situaties worden verkregen met ieder voorkomende soortgelijke melt. Het verschil in voorbehandeling is dat de blinkende zinklaag veel langer moet worden gebeitst als het doffe staal S355 bij gebruik van hetzelfde beitsbad met gelijkblijvende parameters. Van het blinkende gladde zink word minimaal
2 g/m² afdracht ingesteld. Voor het andere materiaal kan een kortere tijd volstaan waarbij ook de afdracht op 2 g/m² ingesteld dient te worden. De behandeltijd van blinkend glad zink kan oplopen tot een factor 4 of 5 keer de behandeltijd van dof verzinkt materiaal.
De juiste tijden zijn niet algemeen te bepalen. Deze zijn afhankelijk van temperatuur, sproeien of dompelen enz. De factor 4-5 keer langer voor blinkend materiaal blijft in stand voor zowel dompelen als sproeien.
Het grote verschil wordt veroorzaakt doordat bij dof materiaal de reactie onmiddellijk begint en bij blinkend materiaal de reactie heel langzaam op gang komt. Het beitsen voorafgaand aan het aanbrengen van de conversielaag is daarmee veruit de belangrijkste stap om te sturen. Alle andere proces en spoelbaden dienen schoon te zijn conform kwaliteitseisen gesteld door de chemieleverancier.
OPTIMALISATIE POEDERCOATPROCES
Binnen WeCoat gebruikt men voornamelijk GSB geaccrediteerde poeders zowel normale als low-bake van gerenommeerde leveranciers. Dit zodat men er zeker van is dat de juiste poedereigenschappen behaald worden en er een constante basis is om de processen goed in te stellen.
WeCoat heeft ondervonden dat er hechtingsproblemen ontstaan als dunne materialen minder dan 2 mm in een doorloopoven worden gemoffeld op 190°C. De vloeifase van het poeder is dan zeer kort door de snelle opwarmcurve van het dunne materiaal. De moffelcurves zijn in eerste instantie hiervoor aangepast van een continu doorloopproces naar een batch proces.
Hierdoor kan WeCoat de temperatuur laten dalen tussen de batches. Door met een lagere starttemperatuur de batch te starten kan men de vloeifase verlengen, dit is de fase waar de poeders de hechting met de ondergrond vormen, bij de normale poeders tussen 120°C en 140°C.
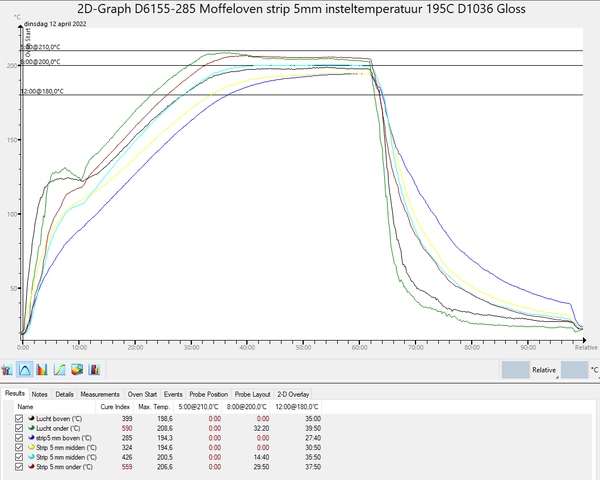
HET PROCES TOEKOMSTBESTENDIG MAKEN
De nieuwe EU-richtlijn met betrekking tot klimaatdoelen voor 2030 zal een grote impact hebben op de verzinkindustrie als geheel. Daarom zijn WeCoat en AD Chemicals een tweede fase van innovatie van
het Duplexcoat proces gestart. In deze tweede fase van optimalisatie is gekeken naar manieren om het Duplex-coatingproces duurzamer te maken door elektriciteit, gas, chemicaliën, water en onderhoudskosten te besparen.
Het belangrijkste energieverbruik binnen het voorbehandelingsproces is:
• Ontvettingsbad op 60°C
• Poedercoating oven op 190°C.
Belangrijkste chemicaliënverbruik en afvalwater:
• Ontvettingsbad (water)
• Beitsbad (chemie).
TEMPERATUUR ONTVETTINGSZONE VERLAGEN
De meeste verzinkers werken met ontvettingsbaden op 60°C. Door deze temperatuur te verlagen met behoud van hetzelfde ontvettingsvermogen kan aanzienlijk worden bespaard op energiekosten.
Daarom heeft WeCoat samen met AD het volgende doel gesteld: De temperatuur verlagen van het ontvettingsbad. Vooral in de sproei installatie waar de chemie tijdens het sproeien snel afkoelt en er veel water verdampt zal de besparing het grootst zijn. Dit was een uitdagende doelstelling en er werd veel getest in de AD-laboratoria, maar het uiteindelijke resultaat is een ontvettingsbad dat werkt bij 35 °C. Het bad draait inmiddels een half jaar waarbij WeCoat ziet dat alleen het gereduceerde dampverlies al resulteert in een energieverbruik dat 30% lager is.
Algehele energiebesparingen van meer dan 60% op het ontvettingsbad zijn gerealiseerd met 30% minder waterverbruik. Een ander voordeel zijn de verbeterde werkomstandigheden: blootstelling door verdampingsverlies wordt drastisch verminderd, wat bespaart op watergebruik, maar ook op het behoud van het gebouw en de omliggende apparatuur.
HET UITHARDINGSPROCES OPTIMALISEREN
Ook in het moffelproces van de poedercoating zijn verbeteringen aangebracht om het proces te optimaliseren. WeCoat is verschoven van continu standaard 190°C naar batch in combinatie met een intelligent geïntegreerd track en control systeem.
Bij het in- en uittreden van balken wordt de temperatuur ingesteld op 120°C en gaan de ventilatoren naar ongeveer 10%. Dit resulteert in het volgende: het temperatuurniveau in de oven wordt gehandhaafd, daarom kan nieuw materiaal direct de moffeloven ingaan zonder eerst in de elektrische oven te gaan terwijl de vorige batch aan het uitharden is. Resultaten:
- Energiebesparing in elektrische oven: 100% (uitgeschakeld)
- Energiebesparende reguliere droogoven (gas): 30%
HET BEITSBAD OPTIMALISEREN
Een normaal verschijnsel bij beitsbaden voor zink is dat, het zinkgehalte in het bad snel stijgt. Beitsbaden mogen maximaal 5 g/l zink bevatten, anders neemt de performantie af. Het bewaken van de hoeveelheid zink is daarom erg belangrijk. Verontreinigde beitsoplossing (zuur) moet behandeld worden in de afvalwaterbehandeling en het beitsbad moet regelmatig aangevuld worden met vers beitsproduct om het procesbad binnen de parameters te houden.
Daarom zijn WeCoat en AD een ontwikkeltraject gestart om de levensduur van het beitsbad te verbeteren. De oplossing is gevonden in een slim regeneratie- en filtratiesysteem. In het kort: een installatie scheidt het zink van het zuur in een gesloten systeem met het beitsbad. Gefilterde beitsoplossing kan daarna worden hergebruikt in de chemische voorbehandelingslijn.
De resultaten van dit systeem zijn duidelijk: besparing op water, minder kalkaanslag en extra besparing op natronloog wat nodig is voor het afvalwaterzuiveringsproces.
Hoewel er uiteraard een investering in apparatuur nodig is om het proces aan te passen aan deze manier van werken, zijn er meerdere grote voordelen te behalen:
• 80% minder kosten voor afvalwaterzuivering
• 20-100K besparing voor gemiddeld duplex-coatingproces
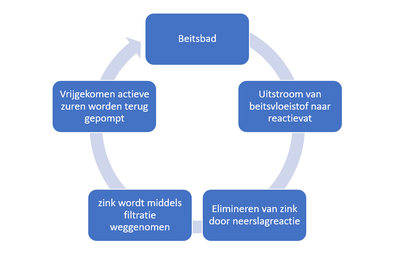
CONCLUSIE
WeCoat en AD zijn er samen in geslaagd om door innovatie en gezamenlijke expertise een reeks verbeteringen te realiseren, wat heeft geleid tot het volgende overzicht van besparingen:
- Vervanging van chroom(VI)
- Besparingen in:
Afvalwaterbehandeling
Proceswater
Chemische consumptie
Energie
AUTEURS: Roland Van Meer (r.vanmeer@adinternationalbv.com) & Norbert Beljaars
MEER INFO: https://www.adinternationalbv.com/nl/