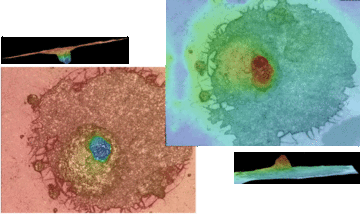
Acier inoxydable : contrôle de la qualité de l'électropolissage
Utilisation du concept de surface développée grâce à l’interférométrie
Les cahiers des charges et le contrôle qualité des finitions de surface de l’acier inoxydable s’articulent généralement autour du paramètre de rugosité arithmétique, appelé usuellement Ra. On peut cependant s’interroger sur l’exhaustivité de ce seul paramètre.
Aujourd’hui, des technologies de pointe permettent d’approcher d’autres paramètres plus pertinents dont par exemple la surface développée (SDr). Ce concept est particulièrement adapté aux finitions électropolies de l’acier inoxydable. En combinant cette technologie à la technique des répliques métallographiques qui permet de prendre une empreinte sur n’importe quelle surface, il est désormais possible de contrôler en laboratoire la qualité microscopique de celle-ci.
Le contrôle qualité ou la quantification de l’état de surface d’équipements neufs à haute valeur ajoutée peut se révéler être un défi tant pour le constructeur que pour le client final. A ce jour, lorsqu’un cahier des charges est établi pour la fabrication d’un nouvel équipement, il fait généralement référence à des paramètres de rugosité tels que la hauteur moyenne arithmétique (Ra), mais également les Rz, Rp, Rv... L’utilisation d’un seul de ces paramètres, typiquement le Ra, équivaut à simplifier l’état réel de la surface. On omet alors une grande quantité d’informations qui peuvent se révéler pertinentes en fonction de l’application finale. Cela peut à terme justifier des différences de comportement vis-à-vis de la résistance à la corrosion ou de la nettoyabilité de l’équipement par exemple.
Il est nécessaire de conserver des paramètres quantitatifs primaires comme la rugosité. Néanmoins une caractérisation approfondie de l’état de surface microscopique devrait être envisagée.
Tout en évitant les surenchères au niveau de la qualité, le contrôle de ces paramètres permettra au constructeur de démontrer, à un certain niveau, son savoir-faire et sa maitrise du procédé de mise en forme et du traitement de surface appliqué.
Au-delà des capacités des palpeurs mécaniques, l’utilisation de la microscopie numérique 3D et de l’interférométrie permet la reconstruction en 3 dimensions de surfaces pour une analyse exhaustive des paramètres.
Le microscope 3D, en utilisant la lumière du visible alliée à un software performant, permet une analyse macroscopique et microscopique de la surface. Les défauts de tailles « importantes » (de l’ordre du micron) peuvent être analysés et caractérisés. La rugosité d’un profil linéaire (Ra) ou d’un profil 3D (Sa) peut être calculée.
L'interféromètre (ou profilomètre) permet de compléter et d’affiner ces résultats par une analyse submicroscopique détaillée de l’état de surface. Basée sur le principe de l'interféromètre de Michelson, cette technologie permet de construire une image extrêmement fidèle de la surface en analysant les zones d’interférences constructives pour déterminer la position géographique de chaque pixel constituant l’image.
Bien que ces deux techniques utilisent la lumière du visible, le traitement de l’information par l’interférométrie rend cette technologie très performante dans l’analyse de surface extrêmement lisse.
Ce type de caractérisation de surface se limite malheureusement à l’analyse de petit échantillon en laboratoire. Il est en effet impensable de transporter et d’utiliser ces microscopes directement sur le terrain au vu de leur sensibilité, aux vibrations par exemple. Une technique de répliques peut donc être mise en œuvre pour permettre l’analyse en laboratoire. Pour réaliser l’empreinte en négatif, un film d’acétate de cellulose est apposé sur une surface à caractériser. Préalablement imprégnée d’un solvant, le film devient élastique. Par effet ventouse, le film d’acétate épouse alors parfaitement la surface au fur et à mesure que le solvant s’évapore. Après quelques minutes, le film retrouve son intégrité et peut alors être décollé. Ce film peut ensuite être observé sous le microscope pour reconstruire une image de la surface inspectée.
Plusieurs applications directes de cette technique d’analyse s’ouvrent aux fabricants ou utilisateurs d’équipements process :
- contrôle qualité à la réception d’un équipement neuf
- contrôle qualité pour la validation d’un traitement curatif mis en œuvre sur un équipement usagé (polissage mécanique par exemple) ;
- Support décisionnel pour déterminer si des traitements de remédiation doivent être mis en œuvre sur des équipements présentant des défauts (griffes par exemple).
A titre d’exemple, les figures présentées dans cet article montrent des analyses de surface sur des équipements neufs et une analyse de défauts ponctuels.
La première image montre une surface en cours de polissage mécanique, lorsque l’opérateur travaille avec des abrasifs de tailles importantes.
La seconde image illustre également le polissage mécanique avec une finition dite “poli miroir". Bien que le Ra soit extrêmement faible (< 0,1 μm), l’interféromètre nous montre une surface présentant de très nombreuses griffes de quelques dizaines de nanomètres. Cette image illustre particulièrement bien la précision que peut atteindre l'interféromètre dans l’analyse de surfaces très fines.
La troisième illustration montre une surface en acier inoxydable après électropolissage.
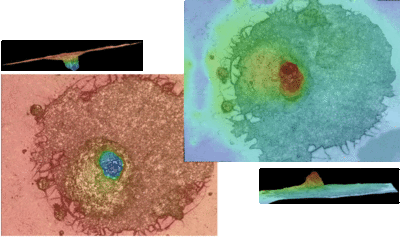
Enfin, la dernière illustration permet de comparer la qualité des résultats obtenus entre l’analyse d’un défaut réel et sa réplique en microscopie. Sur la gauche de l’image, une piqûre de corrosion a été observée et caractérisée sur un échantillon. La réplique de cette piqûre est présentée sur la droite de l’image en négatif. Les valeurs enregistrées entre la réplique et le défaut réel démontrent l’efficacité du système de répliques.