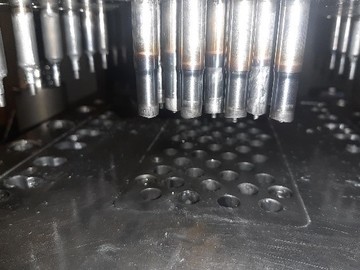
Afsluitende resultaten over Cornet-project DCT4Cut
Het Cornet-project DCT4Cut rond snij- en ponsgereedschap werd in 2019 opgestart en is werd begin dit jaar afgesloten. Na meer dan twee jaar onderzoek werkten Sirris en de VOM hiervoor samen met twee afdelingen van het befaamde Fraunhofer instituut in Duitsland nl IST in Braunschweig en IWU in Chemnitz. Het project verdiepte zich in de voordelen van PM staal, cryogeen diepkoelen en het gebruik van speciale coatings (PVD) op de levensduur van complexe ponsgereedschappen.
Opzet van DCT4Cut
Het onderzoeksproject omvat een aantal werkpakketten rond het gebruik van hooggelegeerd koudwerkstaal voor ponstoepassingen. De term ‘koudwerk’ heeft hier betrekking tot de toepassing nl bewerkingen zoals ponsen uitgevoerd bij kamertemperatuur. Het aantal stalen uit deze groep is zeer omvangrijk en behandelen we hieronder in het kort. Verder heeft het project getracht om de voordelen van een speciale warmtebehandeling nl met gebruik van een cryogene diepkoeling (constante DCT en ‘cyclische’ DCT) en het gebruik van speciale coatings (PVD) op de levensduur van complexe ponsgereedschappen aan te tonen.
Voor deze studie werden vooraf 4 verschillende soorten koudwerkstaal geselecteerd: een veelgebruikt conventioneel koudwerkstaal K110 (1.2379) als referentie, een ESR-geraffineerd staal Caldie en twee poedermetallurgische (PM) stalen nl Vanadis 4E en K390. De ESR- en PM-stalen hebben als voornaamste voordeel de hogere zuiverheid van de kernstructuur (minder insluitsels), de PM-stalen hebben daarenboven ook nog een meer uniforme structuur in de drie richtingen (zgn isotrope structuur). Hun korrelgrootte is doorgaans fijner alsook de aanwezige carbiden t.o.v. ESR en conventioneel gesmolten stalen. De keuze voor deze 4 stalen was gesteund op ervaring uit een vorig project (Cornet-Infiblank) en op ervaring van diverse industriële gebruikers in binnen- en buitenland. Er zijn uiteraard nog vele andere staalsoorten die in aanmerking kunnen komen voor de beoogde toepassing. In het deel over industriële testen kwamen sommige andere staalsoorten ook aan bod.
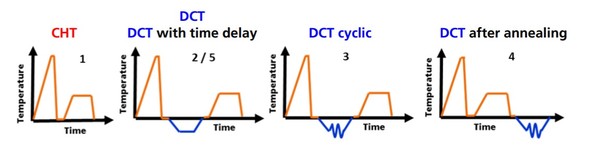
Figuur 1: Verschillende hardingscycli voor testen
De staven waaruit de ponsen gemaakt werden bij een Vlaamse loonharderij gehard waarbij een conventionele hardingsmethode in een vacuümoven werd gecombineerd met een zgn diepkoeling uitgevoerd bij twee bedrijven actief in de industriële koelsector. De beoogde hardheid bedroeg 59+2 HRC.
Teststrategie
Figuur 1 toont schematisch de verschillende mogelijkheden om koudwerkstaal te harden al dan niet met gebruik van een cryogene diepkoeling. Links wordt de conventionele cyclus getoond bestaande uit een austeniteerbehandeling gevolgd door één ontlaatbehandeling doch in de praktijk wordt meestal een drievoudige ontlaatcyclus toegepast. Daarnaast wordt in de tweede grafiek een cyclus getoond maar met gebruik van een diepkoeling tot -196°C direct na het afschrikken. Deze behandeling wordt dus uitgevoerd tussen de austeniteren en het ontlaten. In de derde grafiek wordt een variante behandeling getoond bestaande uit een cyclische diepkoeling waarbij de temperatuur schommelt tussen -80°C en -196°C.De bedoeling van deze cyclische behandeling is van de duur van de constante diepkoeling (24 uren) te reduceren naar 8 uren. Tenslotte is er een zgn ‘post- diepkoeling’ waarbij de cyclische behandeling uitgevoerd wordt na het ontlaten dus op het einde van het hardingsproces. De diepkoeling heeft als voornaamste doel de aanwezigheid van restausteniet gevormd tijdens het harden te verminderen waardoor de hardheid en de maatstabiliteit toenemen.
Volgens de literatuur zou het diepkoelen tevens zorgen voor een toename van uitgescheiden secundaire carbiden waardoor de slijtageweerstand in belangrijke mate stijgt. De vermelde afname van het restaustenietgehalte werd echter niet vastgesteld op de onderzochte stalen omdat een drievoudige ontlaatbehandeling bij het hardingsproces reeds zorgt voor een drastische vermindering. Ook de schijnbare toename van het aantal carbiden kon niet experimenteel bevestigd worden. Tenslotte werden de interne spanningen veroorzaakt door het harden gemeten met en zonder toepassen van een DCT. Vijf metingen met een mobiel X-stralen diffractietoestel werden uitgevoerd op het conventioneel staal nl K110 met twee DCT varianten waaronder een zgn uitgestelde diepkoeling alsook op het PM staal K390. Er kon geen significante af- of toename van de interne spanningen aan het oppervlak vastgesteld worden bij K390 en slechts een lichte toename bij K110 in één richting (zie figuur 2).
Figuur 2: Interne spanning in twee richtingen voor en na DCT
Testen op laboschaal
Een reeks geharde staven werden aangemaakt volgens bovenstaande cycli en nadien grondig gekarakteriseerd op vlak van hardheid, structuur, hoeveelheid carbiden, restausteniet gehalte, scheurvorming na krastesten enz. Nadien werden de staven getest d.m.v. ponstesten op laboschaal bij Fraunhofer IWU in Chemnitz. Een ander deel van de staven werd bij Fraunhofer IST in Braunschweig bedekt met verschillende coatings.
Testen op coatings
Fraunhofer IST heeft vooral de invloed van hardingsstrategie onderzocht nl het toepassen van de diepkoeling hetzij vòòr of na het ontlaten en coaten (zgn post DCT). De coatings bestonden uit geavanceerde PVD lagen zoals WC-DLC en CrTiAlSiN afgezet met en zonder voorafgaande plasmanitreerbehandeling (PN). Deze laatste behandeling wordt niet altijd uitgevoerd maar uit de ponstesten bleek dat de hechting en de weerstand van de coatings toenam alsook de weerstand tegen uitbrokkelen van de snijranden. De invloed van DCT uitgevoerd vòòr het nitreren gaf weinig verschil op vlak van adhesie van de meeste PVD lagen zoals volgde uit de krastesten. De diepkoelbehandeling na het aanbrengen van de TiAlSiN en de CrAlTiSiN coatings gaf echter wel een verschil nl een stijging van de microhardheid en van de Young’s modulus. Voor de ponstesten werden de CrAlTiSiN en WC coatings geselecteerd.
Resultaat labotesten
Om voldoende differentiatie toe te laten werd geopteerd voor een stempel (diameter 5 mm) met een deels hoekige, deels ronde vorm (zgn ‘Dreieck-geometrie’). Het te ponsen materiaal was een roestvast staal met dikte van 0,6 mm, de slaglengte bedroeg 2 mm.
Met deze stempels werden de 4 materialen vergeleken in zowel de klassiek geharde als in de geharde en diepgekoelde toestand en zonder coating. In de conventioneel geharde toestand bleken Vanadis 4E en K390 het minste slijtage aan de hoekpunten van de stempels te geven. Na diepkoelen kon men visueel een geringere slijtage van het snijrand (hoekpunt) vaststellen op het conventioneel staal K110 en op Caldie. De ponsstempels hadden dan meer dan 100000 slagen gemaakt.
Nadien werden nieuwe stempels gehard en onderworpen aan een ‘cyclische’ DCT uitgevoerd bij een Oostenrijkse firma waarbij de temperatuur cyclisch varieerde tussen -197°C en -80°C i.p.v. bij een constante temperatuur van -196°C. Na de ponstesten kon men bij staal K110 en Caldie kon men zoals bij de gewone DCT een vermindering van de slijtage vaststellen terwijl bij de PM-stalen Vanadis 4E en K390 er geen verschil werd vastgesteld.
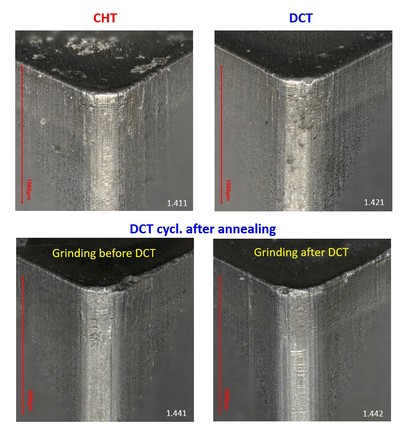
Tenslotte werden er ponstesten uitgevoerd met cyclisch diepgekoelde en gecoate stempels in de 4 staalsoorten. De slijtage werd telkens vergeleken met de niet gecoate toestand. Hierbij stelde men vast dat de slijtage op K110 staal, gehard met DCT en met een CrTiAlSiN coating voorzien van een onderliggende plasmanitreerlaag nagenoeg afwezig was. Eenzelfde resultaat werd bekomen met het ESR-staal Caldie alsook met de andere stalen die eigenlijk ook goed scoorden zonder coating.
Om het effect van het plasmanitreren na te gaan werd een vergelijking gemaakt tussen geharde en cyclisch diepgekoelde en gecoate stempels in Vanadis 4E en K390. De hechting van de CrTiAlSiN coating bleek ook zonder PN stand te houden met afwezigheid van enige vorm van slijtage aan de hoeken van de stempels. De stikstofrijke (nitridische) coatings bleken globaal genomen betere resultaten op te leveren dan de WC-DLC.
Resultaat industriële testen
Als finale stap in het project werden een reeks industriële testen uitgevoerd in beide landen. De bedoeling hiervan was de ervaring op laboschaal over te brengen naar de praktijk. Sirris heeft industriële testen opgestart bij drie Vlaamse bedrijven actief op vlak van ponsen van stalen onderdelen zoals rondellen, profielen en rivetten. De testen werden uitgevoerd op respectievelijk K110 staal zonder coating, CPM4V, een Amerikaans PM-staal, maar met samenstelling aanleunend bij Caldie en bedekt met een nitridische duplex coating. Tenslotte werden stempels in ASP23 zonder coating getest voor het maken van rivetten.
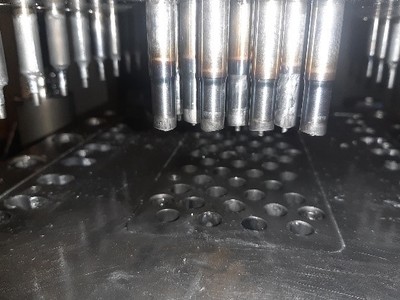
Bij twee testen werd er eerst gehard, nadien diepgekoeld en finaal ontlaten op hoge temperatuur om een nominale hardheid van ca 60 HRC te bekomen. Bij de laatste test werd, aangezien de stempels reeds gehard waren, enkel een diepkoeling toegepast op het einde en een ontlaatbehandeling bij lage temperatuur (post DCT) om de spanningen te verlagen.
Bij de eerste test werd staalplaat in S235 en 8 mm dikte gebruikt om stukjes plaat uit rand te ponsen. De stempels werden vervaardigd uit conventioneel staal K110. Na ca 30000 slagen kon geen duidelijk verschil in gedrag tussen gewone en diepgekoelde stempels vastgesteld worden. De testen werden ook op hogesterkte staal S700 en 1,5 mm uitgevoerd. Hier kon men na ca 70000 slagen wel een verbetering vaststelling voornamelijk op vlak van uitbrokkeling van de snijranden. Een tweede test werd uitgevoerd op stempels in CPM4V voorzien van een duplex coating voor het verwerken van S355 staal en 4 mm dik. Na ca 2000000 slagen werden twee matrijzen voorzien van meerdere stempels vergeleken op vlak van slijtage. De stempels met diepkoeling dienden voor 30 % minder frequent bijgeslepen te worden t.o.v. de niet diepgekoelde stempels.
Bij de laatste test die werd uitgevoerd op post DCT behandelde stempels en roestvast staal als materiaal werd na ca 75000-80000 slagen werd eenmaal een significante stijging van de levensduur vast gesteld. Een herhaling van de test heeft echter geen toename aangetoond zodat hieruit dient besloten te worden dat de post DCT minder effect heeft gehad dan de DCT behandeling vòòr het ontlaten.
HSIC
In Duitsland werden eveneens industriële testen aangevat bij diverse firma’s met naast staal ook vezelversterkte kunststof als ponsmateriaal. De testen uitgevoerd op kunststof bleken echter onvoldoende streng te zijn en werden vervangen door testen op hoge sterkte staalplaat voor de productie van zonnepanelen. Reeds na 1500 slagen kon men een geringere slijtage vaststellen bij de diepgekoelde stempels vervaardigd in K110. Daarnaast werden er ook testen met zgn ultrasnelle impact (afgekort HSIC) uitgevoerd. De ervaring bij IWU uit het verleden heeft nl geleerd dat HSIC-stempels in hoogwaardige koudwerkstalen een beperkte standtijd hebben door de zware belasting tijdens het ponsen. Bij de DCT behandelde onderdelen in S290 en K105 kon de standtijd licht verhoogd worden t.o.v. gewoon geharde onderdelen.
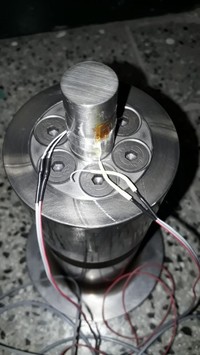
Figuur 5: Stempel gebruikt voor de HSIC testen (Fraunhofer IWU)
Besluit
Het ponsen van staal, inox of kunststof is een complex proces waarbij veel parameters een invloed kunnen uitoefenen op de globale standtijd van het ponsgereedschap. Enkele belangrijke parameters zijn het type koudwerkstaal (conventioneel, ESR of PM), de hardheid, de ponssnelheid, de plaatspeling en last but not least de toestand van het oppervlak en de aanwezigheid van coatings of smering. Daarbij komt dat de definitie van standtijd bij de bedrijven niet overal gelijk gedefinieerd is en veelal door verschillende criteria wordt bepaald. Bijgevolg is het zeer moeilijk om met al deze parameters en criteria rekening te houden. Toch kan men bepaalde tendenzen in het gedrag en de standtijd vaststellen. Vooreerst zijn de PM stalen duidelijk superieur aan de overige staalsoorten, onafhankelijk van de gevolgde hardingsmethode. De diepkoeling heeft zeker zin indien men geen PM staal gebruikt en toch een behoorlijke standtijd wil bereiken. Het voordeel van de behandeling ligt dan voornamelijk bij de reductie van de abrasieve slijtage (uitbreken van snijranden). Indien er adhesieve slijtage (gripperen) optreedt is het gebruik van speciale coatings aan te bevelen. De combinatie van de drie technieken zal zorgen voor een synergie zodat plaatmateriaal met zeer hoge treksterkte en grote plaatdikte kunnen verwerkt worden met behoud van een lange standtijd.
Het project DCT4Cut is een initiatief van het Collective Research Network (CORNET) met de financiële steun van AiF, FGW (Duitsland) en de VLAIO (Vlaanderen) en werd uitgevoerd door Sirris, VOM en Fraunhofer IWU en IST.
Auteur artikel: Guy Claus
Contact : Bart.Teerlinck@sirris.be